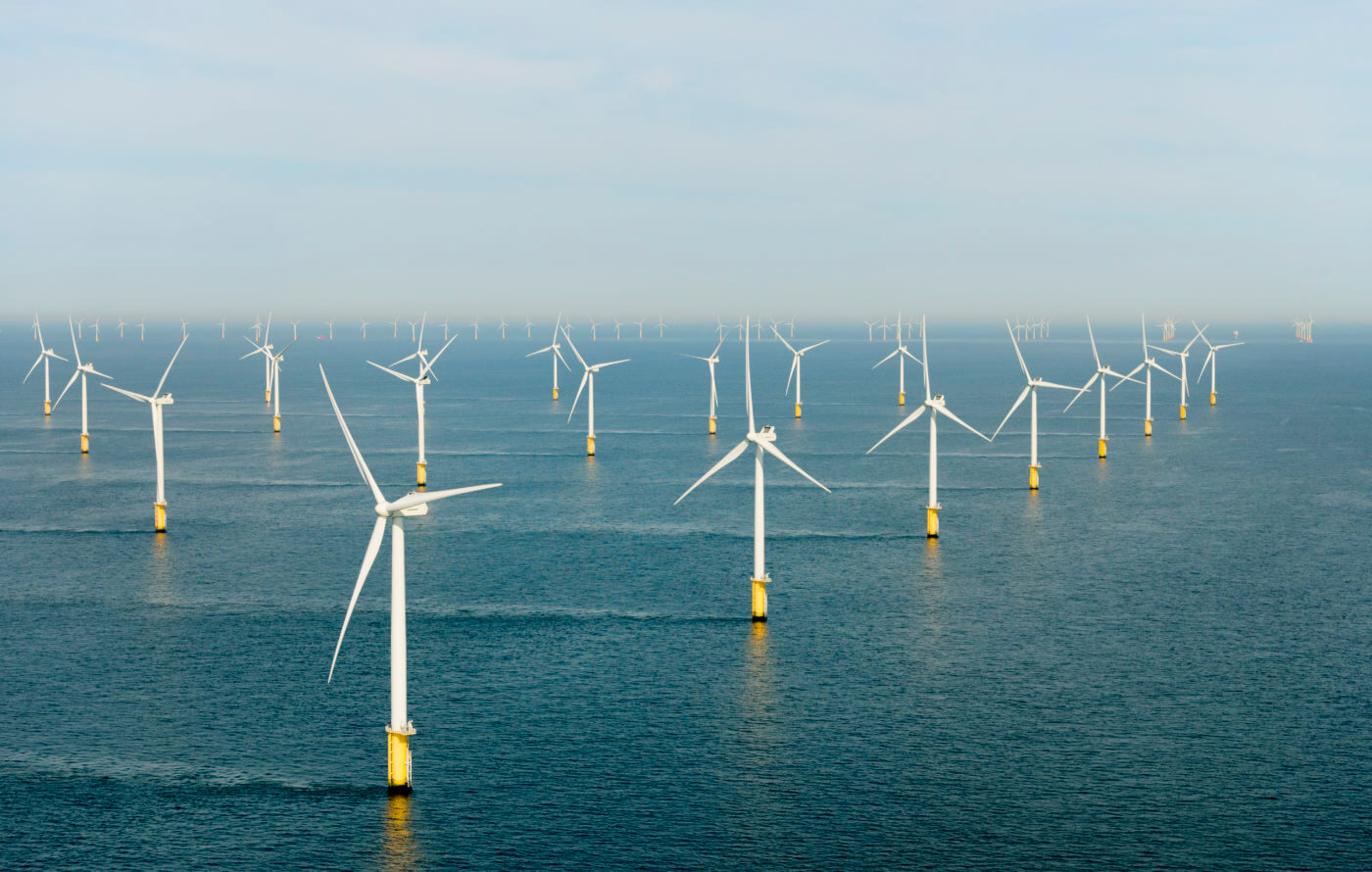
Por qué la industria eólica europea necesita acero descarbonizado
Se prevé que el futuro sistema energético de Europa esté formado por una combinación de energías renovables, energía nuclear y combustibles fósiles reducidos. Es probable que las energías renovables representen una parte importante de esta combinación, especialmente la energía eólica, que experimentará una rápida expansión en las próximas décadas. Algunos estudios sugieren que la energía eólica por sí sola suministrará el 50% de la demanda energética del bloque en 2050.
Se mire como se mire, podemos esperar un boom de construcción de infraestructuras energéticas en las próximas décadas. Los aerogeneradores se fabrican principalmente en acero, una de las industrias europeas de alto contenido energético que se enfrenta a importantes retos de descarbonización.
En todo el mundo, la mayor parte del acero fresco (en contraposición al reciclado) se produce actualmente utilizando altos hornos de combustible fósil, que dependen del carbón de coque o del gas fósil para alcanzar las altas temperaturas y las reacciones químicas necesarias para fundir el mineral de hierro. Actualmente, no hay métodos alternativos para producir acero fresco a escala sin combustibles fósiles, aunque se están experimentando varios métodos alternativos, como los hornos alimentados con hidrógeno y el acero producido mediante electrólisis. A menos que estos métodos alternativos puedan alcanzar la escala y los bajos costes necesarios para mantener la competitividad de los fabricantes de acero europeos, vamos a ver emisiones extremadamente altas por el aumento de la demanda de acero.
La industria siderúrgica europea necesita un marco político adecuado que garantice su transición hacia un funcionamiento neutro desde el punto de vista climático, manteniendo al mismo tiempo su competitividad. Esto incluye la electricidad eólica en una cadena de valor descarbonizada.
La energía eólica, un asunto europeo de larga data
Los gigantescos aerogeneradores modernos habrían causado estupor en Don Quijote. No habría podido atacar sus aspas giratorias como deliraba en la novela clásica del siglo XVII de Miguel de Cervantes, simplemente porque su humilde lanza no habría podido alcanzar las aspas giratorias de estos gigantes modernos.
Europa lleva utilizando la energía eólica desde la Edad Media. Los molinos restaurados en los bucólicos paisajes holandeses nos recuerdan una época en la que la fuerza del viento drenaba el agua de las tierras bajas para evitar las inundaciones. Los molinos de viento también se utilizaban para muchas otras actividades, como moler granos, serrar madera y prensar semillas para obtener aceite. En Castilla de la Mancha, España, algunos de los molinos de viento que inspiraron a Cervantes pueden ser visitados por los turistas que siguen los pasos de Don Quijote. En la sociedad digitalizada de hoy, confiamos en una versión modernizada de esta tecnología familiar para la transición a un nuevo sistema energético. Sin embargo, aunque hemos conseguido aprovechar la fuerza del viento para generar electricidad renovable, el acero que utilizamos para construir estos modernos aerogeneradores no se produce en cadenas de valor descarbonizadas.
El acero está en el centro de la producción de turbinas eólicas
El proceso de construcción de los aerogeneradores requiere cantidades considerables de energía, en parte porque están hechos de al menos un 70% de acero. Las industrias que hacen un uso intensivo de la energía, incluidas las siderúrgicas, fueron responsables del 15% del total de las emisiones de gases de efecto invernadero de la UE en 2015. Estas industrias son cruciales en la transición hacia la neutralidad climática. Producen los componentes básicos para que las sociedades realicen la transición hacia sistemas energéticos más respetuosos con el medio ambiente, y son una fuente esencial de empleo en Europa.
En la actualidad, los aerogeneradores se producen con la herencia de los sistemas energéticos de la Segunda Revolución Industrial y las emisiones de gases de efecto invernadero asociadas. A pesar de décadas de mejoras en la eficiencia, la industria siderúrgica aún está lejos de ser neutral desde el punto de vista climático. A modo de ejemplo, las emisiones ascendieron a 1,85 toneladas de CO2 por tonelada de acero producida en 2020. La Unión Europea es el segundo productor mundial de acero, con una producción de aproximadamente 150 millones de toneladas al año, lo que supone 2,6 millones de empleos directos e indirectos en el bloque. Alemania, Italia, Francia y España son los mayores productores europeos de acero, con más del 50% de la producción total de la UE. La industria siderúrgica europea emite 221 millones de toneladas de gases de efecto invernadero al año, es decir, aproximadamente el 6% del total de las emisiones de gases de efecto invernadero de la UE.
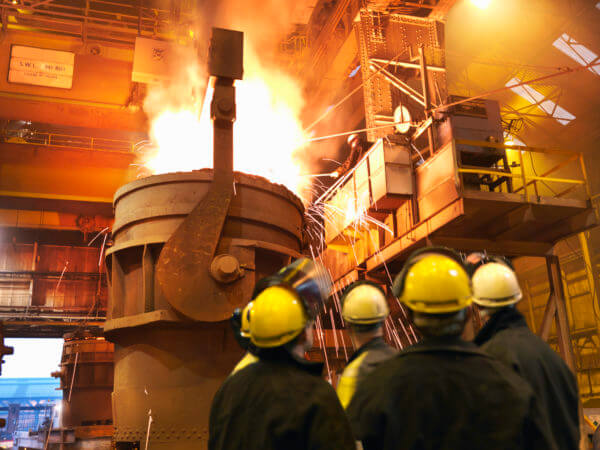
Remscheid, ciudad donde se fabrican piezas para aerogeneradores
Remscheid es una ciudad situada en la zona industrial alemana de Renania del Norte-Westfalia. Una ciudad con un sólido legado industrial y una larga historia de fabricación de herramientas y maquinaria. Por ejemplo, Dirostahl, una empresa familiar con sede en Remscheid, con más de 400 años de tradición de forja. Emplea a unas 500 personas y produce entre 50.000 y 70.000 toneladas de productos de acero al año. En la actualidad, el 50% de su cartera de productos se destina a la industria de generación de electricidad renovable, ya que fabrica ruedas dentadas y cojinetes que son esenciales en el proceso de construcción de turbinas eólicas. Dirostahl es un ejemplo de empresa en la que los conocimientos y los productos casan perfectamente con la visión europea del "Green Deal". Sin embargo, aunque empresas de forja de acero como Dirostahl producen algunos componentes necesarios para construir el futuro sistema energético, no les resulta nada fácil la transición a un modelo de operaciones de bajas emisiones en el actual panorama de políticas, mercados y financiación.
Las industrias que hacen un uso intensivo de la energía son difíciles de descarbonizar porque su demanda energética no puede satisfacerse comercialmente sólo con la electrificación. Una empresa de forja de acero como Dirostahl calienta sus hornos a 1.200 grados centígrados con gas fósil. Forjan grandes piezas de acero (recordemos que estamos hablando de gigantescas turbinas eólicas) que no pueden producirse en hornos eléctricos debido a una combinación de sus dimensiones y de los requisitos de energía del proceso.
Se necesita un suministro de energía fiable, seguro y asequible para forjar esas enormes piezas de los aerogeneradores. En la actualidad, el gas fósil cumple todos esos requisitos. ¿Pueden empresas como Dirostahl desplegar otras tecnologías de descarbonización, como la captura de carbono para reducir las emisiones o el hidrógeno como combustible de carbono cero en lugar del gas natural? La respuesta es sí. Deben desplegar tecnologías de descarbonización o sus operaciones no serán viables en una Europa climáticamente neutra. El reto consiste en crear un ecosistema adecuado en el que las industrias que hacen un uso intensivo de la energía puedan pasar a operar con bajas emisiones sin perder competitividad frente a los productores de fuera de la UE que no están obligados a cumplir objetivos ambiciosos de descarbonización.
De la teoría a la práctica
Demos un paso atrás. Empresas como Dirostahl han conseguido modernizar sus operaciones y mejorar los sistemas energéticos para reducir las emisiones y la contaminación a lo largo del tiempo. En el caso de Dirostahl, los antepasados del actual propietario eran casi todos herreros desde el siglo XVI. Es decir, un siglo antes de que Don Quijote y su caballo acabaran tirados en el suelo tras dar una estocada a la vela de un molino de viento en funcionamiento.
Una empresa con 400 años de tradición de forja familiar debería ser lo suficientemente resistente como para hacer la transición a un sistema energético de bajas emisiones. Al fin y al cabo, pasó del carbón al petróleo pesado a mediados del siglo pasado. En los años 70, pasó del petróleo pesado al gas natural. En la actualidad, utilizan la tecnología más avanzada de forja de acero y han adoptado medidas de eficiencia para reducir el consumo de energía. El siguiente paso, la adopción de combustibles con cero emisiones de carbono o la tecnología de captura y almacenamiento de carbono, es más disruptivo y caro.
Dirostahl consume unos 200 GWh al año de gas natural. Si utilizara hidrógeno renovable para satisfacer su demanda energética, necesitaría 20 toneladas de hidrógeno al día o el equivalente a 30 MW de capacidad de electrolizadores instalados. La instalación de electrolizadores in situ plantea enormes dificultades. Algunos de ellos son el funcionamiento de los electrolizadores, el espacio adicional requerido y, por último, el sistema de transmisión de electricidad necesario para suministrar la energía renovable al emplazamiento. Por no hablar del aumento de los costes de producción asociados, que son prohibitivos en el mercado mundial actual.
En la actualidad, no hay oleoductos que suministren hidrógeno a la región, por lo que es difícil considerar la compra de hidrógeno a un tercero en un futuro previsible. No hay tuberías para transportar el CO2 a un lugar de almacenamiento geológico adecuado si se elige la captura y el almacenamiento de carbono como tecnología de descarbonización preferida en la región de Renania del Norte-Westfalia. Sin embargo, un estudio reciente del Instituto Wuppertal para el Clima, el Medio Ambiente y la Energía ha revelado que una infraestructura de tuberías de CO2 para transportar a los lugares de almacenamiento en el extranjero podría resultar decisiva para descarbonizar todo el sector industrial de la zona. De hecho, 30 de las 50 fuentes puntuales de CO2 identificadas en Renania del Norte-Westfalia podrían conectarse para la captura y el almacenamiento de carbono, lo que mitigaría el 97% de las emisiones del sector. El desarrollo de los conductos de hidrógeno y CO2 necesarios es una prioridad clave para el Gobierno de Renania del Norte-Westfalia, que ha elaborado su propia Estrategia de Gestión del Carbono como primer paso fundamental para descarbonizar el sector industrial de la región.
¿Cuáles son las necesidades críticas para acelerar la descarbonización de la industria siderúrgica?
La infraestructura es uno de los aspectos clave necesarios para que las industrias que hacen un uso intensivo de la energía realicen la transición a sistemas de bajas emisiones. Los combustibles con cero emisiones de carbono, como el hidrógeno, deben ser transportados desde los productores o las terminales de importación hasta los usuarios finales. Con la propuesta del Paquete del Gas, publicada en diciembre de 2021, la Comisión Europea intenta crear el marco normativo para un sistema de gas descarbonizado. La infraestructura necesaria para transportar las moléculas de dióxido de carbono capturadas desde las instalaciones industriales hasta los lugares de almacenamiento geológico adecuados debería contar con el apoyo de las normativas RTE-E y RTE-T.
También es necesaria la comercialización de tecnologías como los quemadores de hidrógeno con la capacidad necesaria para las industrias de alto consumo energético. Sin ello, no existe un argumento comercial positivo para que estas industrias realicen la transición a los combustibles de carbono cero. En un reciente acto de descarbonización industrial organizado por Future Cleantech Architects, el Dr. Roman Diederich, Director General de Dirostahl, indicó que la transición del gas natural al hidrógeno renovable se traduciría en un aumento de entre 700 y 800 euros por tonelada de acero, lo que haría que sus productos no fueran competitivos en un mercado globalizado.
La descarbonización de la industria siderúrgica es crucial para garantizar que toda la cadena de valor de la electricidad eólica sea baja en carbono. El apoyo de los Estados miembros al desarrollo de infraestructuras de hidrógeno será esencial en los próximos años. Esto también se aplica a la infraestructura de transporte de CO2. Políticas como los Contratos por Diferencia de Carbono (por ejemplo, SDE++ en los Países Bajos) serán fundamentales para cerrar la brecha de comercialización de las tecnologías descarbonizadas y hacer realidad los proyectos de descarbonización.
La noticia alentadora es que el nuevo acuerdo de la coalición alemana ha reconocido la necesidad de un marco de apoyo que permita la transición hacia una industria neutra desde el punto de vista climático, la creación de mercados líderes y la necesidad de precios competitivos de la energía para la industria.
Otra pieza del rompecabezas de la descarbonización estará en su sitio cuando los gigantescos aerogeneradores que generan parte de la electricidad renovable de Europa se fabriquen con acero bajo en carbono o renovable. El largo romance de Europa con los molinos de viento se llevaría a un nivel en el que se aprovecharía la fuerza del viento de forma realmente sostenible.